EIA of Textile Industry talks about environmental impact assessment of textile in detail. Before knowing about the EIA of Textile Industry we should know about the textile industry first.
About the Textile Industry
A textile is a substance created from fine fibres or filaments that have been spun into yarn and knitted into cloth. The Latin term for weaving, texere, is where the word “textile” originates. So, materials used to make textile threads are those that are used to weave textiles.
The textile sector is India’s second-largest employer after the agricultural sector. It is the only industry in textiles that has produced significant employment for both skilled and unskilled labour. It is one of the most ancient sectors in the Indian economy, having existed for many years. One of the most environmentally destructive sectors in the world is the textile industry.
China and India, among the developing nations, are anticipated to account for 45 and 20% of world trade, respectively, by 2014. Since 1995, China has been the world’s top exporter of textiles and apparel when the textile and apparel sectors are combined. According to the WTO trade statistics 2010, the EU, the United States, India, Turkey, Pakistan, Indonesia, Thailand, and Vietnam all rank among the top 15 exporters of textiles and garments.
This industry uses around 2000 distinct kinds of chemicals. It contaminates freshwater and consumes it. Over 7 x 105 tonnes of synthetic dyes are manufactured annually worldwide, and it is believed that over 10,000 distinct dyes and pigments are employed in industrial settings. There are 1.3 million tonnes of dyes and pigments used and produced by the textile industry, the majority of which are synthetic.
What is EIA and what do you mean by EIA of Textile Industry?
EIA (EIA of textile industry )stands for Environmental Impact Assessment. A project’s or development proposal’s important environmental impacts are evaluated using a tool called an environmental impact assessment (EIA). The National Environmental Policy Act of 1969 in the United States is the source of this methodical approach that seeks to detect and anticipate the probable effects of human activity on the biophysical and human environment (which became law on January 1, 1971).
EIAs ensure that decision-makers for projects consider the likely effects on the environment as early as feasible and work to avoid, mitigate, or counteract those consequences. By doing this, it is ensured that suggestions are adequately understood before decisions are taken.
Life cycle assessment (LCA), a methodical scientific method for examining the environmental implications of a product or service across its full life cycle, may be the best way to determine the overall impact on the environment of a textile product or process.The EIA of textile industry framework might be helpful for assisting textile and apparel firms in reducing their environmental impact. The SustainTex system tool kit is introduced and detailed after a review of current EIA techniques.
Now what is this SustainTex system tool kit
A set of EIA tools called SustainTex has been created by the authors in order to assist textile and apparel industries in successfully conducting an EIA process, and it is offered here. Such tools are derived from conventional EIA methodologies that have been modified to account for the specific environmental, technological, process, and technical requirements of the textile and apparel industry. Two methods—field surveys (conducted at a number of textile and apparel industries) and the input of an assessment panel—have been used to develop the SustainTex system tool kit from a methodological standpoint.
Explore Environmental Management System Solutions
Find top machinery, plants, tools, resources, companies, and consultancy for comprehensive EIA Solutions.
EIA of Textile Industry & LCA
To ensure that all pertinent impacts are included and to prevent overlaps, distinct forms of environmental impact, such as toxicity, ozone depletion, and climate change, are categorised in LCA. Regarding which environmental impact categories that are relevant, there is currently broad agreement and mature understanding among various LCA applications, such as the European Product Environmental Footprint (European Commission 2017a) and the UN Environment Life Cycle Initiative (UNEP 2016), as well as between LCA and other environmental schemes, such as the UN Sustainable Development Goals (United Nations 2015b) and the Planetary Boundaries (Rockström et al. 2009). There is also general agreement that the most pertinent effect categories should be stated for a certain product or organisation.
Data on six environmental effect categories—climate change, water consumption/depletion, toxicity, eutrophication, land use and indicators connected to it (such as land use change and biodiversity), as well as energy use—were gathered. According to the European Commission 2017b and Roos et al. (2015), these address the primary environmental effects of the textile industry, to which fibre manufacturing may significantly contribute. In addition, other impact categories that are frequently considered in LCAs of textile products frequently produce patterns that are similar to those for climate change, as the burning of fossil fuels is a significant driver of these impacts as well. For instance, see the similarities between the results for climate change and acidification in Roos et al (2015).
Types of Fibre and Raw materials
The textile industries use a variety of fibre types that are either created manually or are obtained from nature. Dresses, towels, blankets, and other products are made with these fibres. Some of these fibres were well-known and utilised both in modern and pre-modern times. In recent years, other fibres have grown in significance to varying degrees. All of these fibres’ capacity to be spun, availability in sufficient quantities, cost or economy of production, and consumer desire for their qualities are the elements that have an impact on their development and use.
In any textile sector that is production-oriented, raw material is a special kind of substance. It is essential for high-quality fabric manufacture and continuous production. Cotton, jute, wool, raw silk, and synthetic goods are the main raw materials used in the textile industry. Textile raw materials are chosen in accordance with the company’s manufacturing strategy, whether it be a composite mill or only a spinning, weaving, or dyeing/finishing operation.
Different kinds of textile raw materials
- Textiles
- dyestuff
- chemicals and
- auxiliary materials
The available textile fibres and the raw materials for the fibre feedstock are categorised in Figure. The image also shows some examples of yarn and fibre brands and how they relate to various fibre groupings. The emphasis has been on companies with some sort of sustainability profile, while other companies are also included. Clarifying the distinction between fibre types and brands in the listing of brands makes it easier to understand the expanding number of brands and their connections to fibre groups and feedstock origin.
An overview of the several forms of fibre, the raw materials, market shares, and some real-world fibre and yarn brands. Although not directly proportionate to the market shares, the sizes of the fibre group boxes show their relative market shares.
Struggling with Textile Waste issues? Connect with top consultants specialising in EIA in textile industry.
Connect NowReinforcement for composite materials using natural fibres
Natural fibre composites are composite materials that contain reinforcing fibres made from renewable and carbon-neutral resources like plants or wood. NFCs are used in moulded products such as large diameter piping, equipment housings, and roofing for affordable or low-cost housing that require moderate strength for satisfactory performance. Natural fibre composites, which use bio-based and renewable sources to substitute synthetic materials, are classic examples of sustainable resources for industrial uses. The materials have the potential to be economically advantageous for equivalent structural qualities, they can be grown in controlled environments or farms, and they can significantly reduce carbon footprints.
The hydrophilic characteristic of natural fibres, which necessitates chemical treatment to enhance their moisture-related properties, limits their use to interior structures. Undoubtedly, natural fibres are viable sustainable alternatives to synthetic fibres for a variety of textile and non-textile applications. Natural fibre composites have significant advantages for the environment.
It is possible to improve the properties of natural fibres and subsequently the properties of hybrid composites by altering their physical characteristics chemically and combining them with polymers and other synthetic materials. By combining fillers with natural fibre, hybridization improves the mechanical properties of composite materials. Several elements, including the reinforcement’s volume or weight, the fibres’ alignment, dispersion, orientation, and aspect ratio, the adherence of the fibres to the matrix, the use of additives,
Natural fibres could eventually take the place of synthetic fibres in flooring, cladding, walls, and architecture. Sisal, flax, hemp, and wool are utilised in Mercedes-Benz components as well as the inside and exterior of automobiles. The mirror housing, paperweights, projector covers, helmets, and other items all use the coir/polyester-reinforced composites. The usage of kenaf, cotton, ramie, jute, and rice husk fibres in garments, fishing nets, packaging materials, ropes, and sewing threads is also rising. Natural fibres come from a range of plants and animals (hair, chicken feather). The plant-based fibres are made up of waxes, cellulose, lignin, hemicellulose, pectin, and other water-soluble materials.
Important characteristics of natural fibres appropriate for composites and various application areas are covered in the section below:
Cotton
In terms of the textile industry, cotton (Gossypium) is one of the most important agricultural crops, accounting for the lion’s share of the market. The Malvaceae family and Hibisceae subtribe are the ancestors of the fibre. In tropical and subtropical areas, cotton is typically grown, with China being the leading producer, followed by India and the United States. The most well-known and widely used cotton species are pima cotton (Gossypium barbadense) and upland cotton (Gossypium hirsutum). It is a popular option for summer clothes and accessories due to its comfort, moisture-wicking, and hydrophilic qualities. The potential of cotton for the creation of composites for industrial purposes has lately come under investigation.
Hemp
In general, European and Asian locations are where hemp is grown. It is a species of plant. The fibre has a diameter of about 2 cm and may reach heights of between 1.2 and 4.5 metres. Hemp is made up of an inner layer surrounded by a bast fibre outer core, which is joined to the former by a pectin-like material. After the hemp has been harvested, the woody core and bast fibres are mechanically separated. After being separated, the woody core is cleaned to remove the required core content, and it can then be cut into the required size. Yarn or bundles are produced once the bast fibres have been separated. In addition to eco-friendly bags, ropes, garden mulch, composite building materials, and animal bedding, hemp fibre is utilised in a wide range of textile and non-textile items.
Two procedures, retting and burning, are used to remove the flax fibre and change its characteristics. Pectin is degraded by the employment of enzymes during the retting process, which separates the fibres. In addition to being utilised in furniture, household textiles, and items for interior decoration, flax fibre is widely employed in the creation of linen.
Silk
Natural fibre made from animal products, silk (Bombyx mori), is taken out of silkworm cocoons. China, South Asia, and Europe are the three regions that produce the most silk. Fibre is a chosen choice as a luxury material for expensive, high end range of garments and fashion products due to its extraordinarily brilliant features, which include good mechanical strength, extensibility, and compressibility.
Bamboo
Due to the longitudinal orientation of the fibres, bamboo is also known as natural glass fibre. The deep Chinese woodlands are home to 400 different species of bamboo. Fibre is an excellent reinforcement material for polymeric materials, bridges, traditional boats, and other structures due to its lightweight, low cost, great strength, and stiffness.
Sisal
Typically, sisal is grown in South Mexico and Brazil. The fibre is made up of a rosette of leaves and can reach heights of 1.5 to 2 metres.Sisal fibre is widely used for a variety of textile and non-textile applications due to its good mechanical qualities, such as the fibre core of the steel wire cables used in elevators, the automobile industry, the shipping industry, civil constructions, etc.
Pineapple Leaf
The abundantly grown leaf fibre that results from the crop waste left over from pineapple cultivation is known as pineapple leaf fibre. With 20–30 clustered leaves, the little tropical plant has a height of 1-2 m. Multicellular and lingo-cellulosic pineapple leaf fibres. The fibre has strong mechanical qualities, which makes it a popular choice for a variety of uses, including airbags, conveyor belt cord, textile, matting, construction, and vehicles.
Find and connect with leading companies specialising in EIA solutions.
Get Connected Today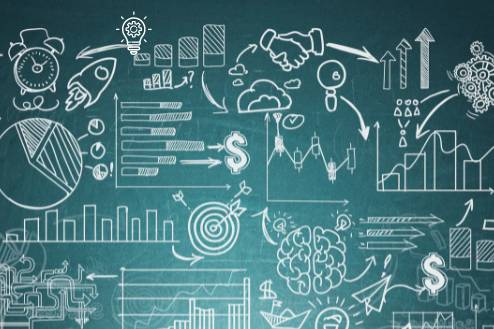
Cotton Textile Industry
When it comes to textile applications, cotton commands a large market share, but the fibre cannot be regarded as sustainable due to its intensive use of water, pesticides, fertilisers, and hazardous chemicals, which has a negative impact on the environment and the economy.
Although cotton is one of the largest natural fibres and has a significant market share in textile items, its production necessitates the heavy use of pesticides, growth fertilisers, chemicals, and water, which has a negative impact on the environment and the economy.
Cotton cloth manufactured in a composite mill.
Additionally, cotton and synthetic fibres dominate the primary markets, but because of the appealing qualities of other natural fibres, textile firms are already using them and will continue to do so in the future. The resurgence of these fibres in the industrial sector is the start of a sustainable strategy, and these developments aid in the preservation of our world. Also It is well recognised that cotton production has a negative impact on the environment. In the cultivation of cotton, the use of pesticides and irrigation results in the release of hazardous chemicals that harm the environment and human health. Cotton farms require a lot of water, hence irrigation causes water stress.
In addition to replacing cotton, some resource-efficient fibres, including hemp, flax, organic cotton, bamboo, jute, kenaf, ramie, sisal, and coir, are doing so because they are biodegradable, have excellent performance profiles, are sustainable, are lightweight, and are economically viable.
Impact of Cotton Fibre on Climate
The average climate impact of cotton fibres is estimated to be between 0.5 and 4 kg CO2 equivalents per kg of fibres (excluding CO2 sequestered in the fibre), but findings up to roughly 6 kg CO2 equivalents are not out of the ordinary. As a result, the variations range by about an order of magnitude. Additionally, when compared to conventional cotton, organic cotton generally has a slightly reduced climate impact13, mostly because fewer artificial fertilisers are used, whose production is CO2 intensive (see, for example, Kalliala and Nousiainen (1999) and Cherret et al. (2005)). According to literature on energy use, producing cotton fibre requires between 12 and 55 MJ per kg of fibre, although database data estimates up to roughly 90 MJ/kg.
The performance of various fibres as well as what are regarded as important environmental characteristics of the textile industry may alter throughout time. The explanation of two hypothetical future challenges—or difficulties that will be solved—is provided below. 1. Increasing the use of renewable energy sources in the energy system Figure illustrates how the consumption of power and heat during the textile production processes, from fibre to garment, contributes significantly to the climate effect of the textile life cycle. Future predictions indicate that the usage of renewable energy sources (such as wind and solar) will rise while the use of fossil energy sources (such as petroleum, coal, and natural gas) will decline. Although anticipated, this transition has not yet taken place: in 2017, the world’s use of fossil fuels climbed and carbon emissions increased for the first time since 2014. (IEA 2018). Fossil fuels provide more than 70% of the additional energy needed in the world. Even though there is uncertainty regarding the timeline for the anticipated switch to renewable energy sources and sustainability issues, such as the use of conflict minerals in the manufacture of solar panels, the future is one in which energy will be produced at a significantly lower environmental cost. The contribution of different life cycle periods, may then alter significantly, and could have an impact on the climate or, to put it another way, the relative importance of the climate impact related to the production of natural fibre feedstock and bioenergy used throughout the garment life cycle may increase (Godfray et al. 2010.2). At a bigger scale, the by-products of regenerated fibres become difficult to handle. One of the most important environmental factors in the manufacture of viscose and other regenerated fibres is the substantial consumption of sodium hydroxide and sulfuric acid. These substances are required for the process and often come out as sodium sulphate as a byproduct. About 1.3 tonnes of sodium sulphate will be created for every tonne of viscose fibres produced; this means that the by-product is more abundant than the intended product (Shen & Patel 2010). Today’s cosmetics industry, which employs sodium sulphate to make soap and related items, can benefit greatly from this by-product. Though the market is currently almost saturated, a substantial scale-up of these regenerated fibres will probably result in a large amount of these by-products going to waste. There are further varieties of regenerated fibres, such as lyocell, which is spun using the recycled solvent NMMO (Shen & Patel 2010). Here, the issue with a lot of by-products is not a barrier to scaling up.
Pollution generated by the textile Industry
The impact of the textile industry’s pollution on the environment is significant, and the causes are clear-cut. The average amount of clothing that a person purchases annually has dramatically increased in recent years. According to a McKinsey & Company study, the quantity of garments manufactured annually has doubled since 2000 and surpassed 100 billion pieces for the first time in 2014. The Lenzing group estimates that 95.6 million tonnes of textiles were consumed globally in 2015. Because of how much money the fashion business makes, its effects on the environment may be severe and harmful.
Water pollution, air pollution, and solid waste pollution are the main environmental issues that the textile sector contributes to. Environmental damage and human illness are both significantly exacerbated by textile waste. The known carcinogen chlorine is organically bonded in around 40% of colourants used worldwide. Given how many disinfectants, particularly chlorine, react with when present in effluent from the textile sector, all organic compounds are a major source of worry. Chemicals can affect human life and vaporise into the air we breathe or are absorbed via our skin. These substances manifest as allergic reactions.
Water pollution
Every day, the textile sector consumes millions of gallons of water. That’s because washing the fibre, bleaching, dyeing, and finally cleaning the completed product often need 200 litres of water to produce 1 kg of cloth.Although there is high usage, the issue is more frequently that waste waters are not treated to eliminate pollutants before being released into the environment. As a result, some studies claim that the processing and dyeing of textiles causes 20% of all freshwater pollution. While processing of synthetic and woollen fabrics often produces acidic effluent, cotton-based textile manufacturing facilities typically produce alkaline waste water. The excessive water and waste output during the textile manufacturing process is to blame for the toxicity of aquatic life. In addition to being dumped into water bodies, many people eat substances like formaldehyde, chlorine, and heavy metals while going about their daily lives.
Solid Pollution
Additionally, the textile sector generates a lot of solid waste.
90 million pieces of clothes each year are dumped in landfills worldwide.
Additionally, the trash generated pollutes the environment when it enters water bodies. Pollutants that wind up in landfills include some of the following:
- Lint, fibre scraps, trimmings, and packaging waste generated during the preparation of the fibre
- Sludge produced and kept during the treatment of waste water
- Containers for flock, chemicals, and dyes used in finishing and dyeing woven fabrics
The several types of pollutants that the textile industry releases into the environment are growing hazardous for both the environment and people.
A new strategy for the creation, use, and disposal of clothing is now unavoidable.

Explore the Best Textile Waste Machinery and Plants for your Industrial Needs.
Connect TodayAir Pollution
Studies indicate that the garment sector is the second-largest industrial polluter, contributing 10% of the world’s carbon emissions.
In particular, the textile industry contributes to air pollution by producing nitrous oxides and sulphur dioxide during the energy production process, volatile organic compounds (VOCs) during coating, curing, drying, wastewater treatment, and chemical storage, and aniline vapours, carrier hydrogen sulphide, chlorine, and chlorine dioxide during dyeing and bleaching.
Standards for discharge of effluents from the Textile Industry by CPCB
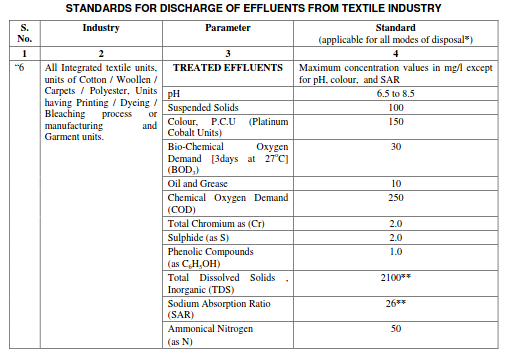
Management of Textile Waste
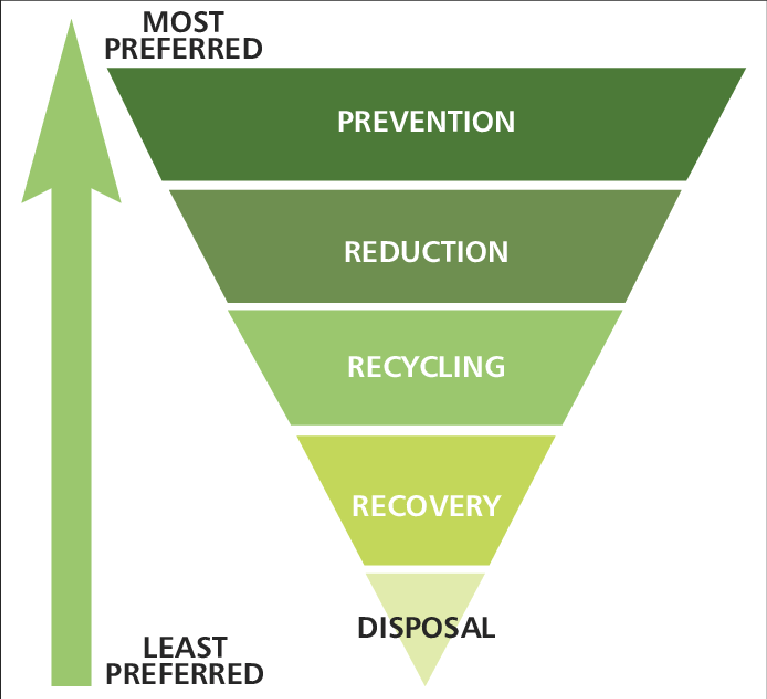
Regeneration/Recycling
Reclaimed/recycled fibres can be used to make cleaning cloth, yarns that are untwisted and respun into new yarn kinds, mattresses, and wadding. Regeneration is a different procedure that uses heat and chemicals to recreate fibre from a natural source. Several well-known companies that create textile fibres from wood include Tencel, Lyocell, and Seacell. After the trees are cut, the timber is reduced to tiny pieces and processed with chemicals, high temperatures, and pressure before being spun into a textile thread. These are applied to the production of durable fabrics.
Composting
Manufacturers now have a huge opportunity to think about degradable/compostable textiles thanks to growing knowledge of the harmful effects of non-biodegradable synthetics. These days, products like diapers, wipes, agro-textile mulching sheets, and car interiors are made to be recycled back into the natural world after their useful lives. The preferred materials today are non-wovens and disposals. Focusing industry research on materials with a 100% natural origin that may completely dissolve when disposed of in landfills at the end of their life cycle will be profitable. Both natural and regenerated fibres can be processed using this technique. There are now PLA biodegradable polymers on the market.A polymer made from corn is called polylactic acid. Improvements are made to the natural antibacterial property, which is subsequently utilised in medical textiles. This cloth can be composted or degraded when dumped in a landfill. Numerous experiments are being done to create composts from chemical-free post-industrial waste and use it as bio-manure on plants. The medium can be strengthened and enriched with useful microorganisms to make it more nourishing for the soil, plants, and water bodies.
Textiles used for technical purposes
Before being transformed into the necessary product for a purpose, textiles were first made and then evaluated to see if they were suitable for the intended application. In contrast, the types of fibres, yarns, and functional finishing that are used rely on the characteristics that the final product must have.Currently, Technitex, or technological textiles, is pictured as a huge banyan tree with connections between all application zones in the main bark. For filtering, recycled fabrics are employed. Automotive interiors, agrotextiles, geotextile reinforcement, acoustics, building construction textiles, upholstery, package textiles, and food packaging materials are further applications for recycled fibres.
Reduction at Source
The initial step in an integrated waste management system should be source reduction to produce little to no trash in the majority of situations. For instance, preventing the development of waste, reusing waste internally, reusing in other products, and so forth. Burning solid waste is a technique for recovering thermal energy. For instance, the heat value of PP is equal to that of gasoline. Short, shredded, or loose textile waste can also be repurposed to create tasty fuel. However, the emissions from incineration chimneys include organic substances that have the potential to harm both people and the environment, including dioxins, heavy metals, acidic gases, and dust particles. Disposing of the leftover ash, which probably contains a harmful concentration, is a problem as well.
Dumping grounds
In a thorough waste management system, it ought to be the very last resort. Leachate, which has the potential to contaminate both surface and groundwater sources, is produced as a result of the breakdown of textile waste in landfills. Methane gas, a key greenhouse gas that contributes significantly to global warming but can be used if trapped, is another result of landfill decomposition. Significant amounts of ammonia and methane are produced during the breakdown of organic fibres and yarns, such wool. Ammonia is exceedingly dangerous in both terrestrial and aquatic environments, and it can be fatal in gaseous form. It has the capacity to increase the quantity of nitrogen in drinking water, which may be detrimental to people.
Struggling with textile waste buying and selling issues? Connect with textile waste buyers and sellers here.
Buyer Listings Seller ListingsEnergy generation from Textile Industry Waste
Textile effluent must be handled using any other environmentally friendly sustainable methods in order to lessen its negative environmental impacts. Utilising textile wastewater as a source of renewable energy and creating electricity from the effluent is one of these environmentally good options. Industrial waste serves as a biodegradable substrate in MFCs, which transform chemical energy into electrical energy. The biodegradable substrates are oxidised by the microorganisms in MFC to produce protons and electrons. Electricity produced by the electron flow in the MFC is usable for further purposes. In order to lessen or completely eliminate the negative effects of textile effluent on the environment, MFCs must be used to generate electrical energy from the wastewater from the textile industry. MFCs have a wide range of possible uses, including the production of biohydrogen, wastewater treatment, and biosensors.
In the anodic chamber, microorganisms oxidise substrates to create electrons and protons product during the oxidation process that results in carbon dioxide. The cathode receives electrons from the anode (negative terminal) through an external circuit to (positive terminal). Protons go through electrons mixed with the proton/cation exchange membrane to form if oxygen is present, to produce water; if ferricyanide is present, to produce ferrocyanide.
Consequently, a positive current moves from the positive terminal to the negative terminal, and the electrons move in the opposite way . This is how microorganisms produce energy in MFCs , as demonstrated in Figure.
Schematic diagram of two-chamber microbial fuel cells
Since there is no net carbon dioxide emissions from the oxidation of organic carbon sources in MFCs, there is no requirement for expensive catalysts or intensive fuel pre-processing. These are the key advantages that MFCs have over hydrogen fuel cells, although power output from MFCs is currently constrained by high internal resistance or cathodic reaction efficiency, and the viability of scaling up MFCs is constrained by the high cost of membranes.
Summary
This article is based fully on the EIA of Textile Industry and how this assessment helps to create a sustainable environment. Industry can enhance their knowledge of the art of evaluating the environmental impact of fibres, gain a more nuanced understanding of fibres and their environmental performances, and thereby improve design, selection, and sourcing. Industry can also contribute to greater knowledge by enhancing transparency and knowledge-sharing, and enhance communication around the environmental benefits and drawbacks of fibres.
For instance, policy makers can gain a better grasp of how fibres’ effects on the environment connect to and relate to the effects of the final product’s life cycle. Additionally, they can perceive the overall absence of publicly accessible data as well as the variety and inconsistency of procedures as motivation for metric and method standardisation as well as legislation that includes data gathering.
We’ve seen here the by-products of the waste, generated by the Industry and their applications like energy generation. The pollution and waste generated from the textile industry and management of the waste. We’ve also discussed the use of natural fibres in making composite materials which are used in moulded products such as large diameter piping, equipment housings, and roofing for affordable or low-cost housing that require moderate strength for satisfactory performance. Types of pollution caused by the Industry is discussed and there are some standards given by CPCB (Central Pollution Control Board) of effluents which are discharged by the Industry, as also mentioned in this article. Life Cycle Assessment (LCA) practitioners and researchers can view the identified data gaps as opportunities for future research on how to enhance the environmental assessment of textile fibres. They can also become aware of methodological differences between case studies and the current methodological shortcomings of LCA.
FAQs
Ques 1:Write a short note on the greenhouse gas emission by the textile industry.
Answer : According to the European Environment Agency, textile purchases in the EU in 2017 generated about 654 kg of CO2 emissions per person.
Millions of producers and billions of consumers worldwide participate in the highly globalised textile industry. The industry employs 1.7 million people in Europe, and each European consumes 26 kg of textiles annually on average. Clothing, footwear, and home textiles are the fourth-highest or fourth-worst ranked pressure category for use of main raw materials and water when considering supply chain pressures from an EU consumption perspective (after food, housing and transport). In terms of land use, it ranks second, while in terms of greenhouse gas emissions, it is fifth.
In other parts of the world, where most of the production takes place, there are more pressures and effects associated with the consumption of clothing, footwear, and home textiles in Europe. This is true for 85% of the use of fundamental raw materials, 92% of the use of water, 93% of the usage of land, and 76% of the emissions of greenhouse gases.
Ques 2: List some popular toxic textile chemicals and their field of application.
Answer:
Name of toxic chemicals | Used as/in |
Tri-butyl tin oxide (TBTO) | Biocide on hosiery and fabrics |
Non-ionic surfactants | Detergents in textile preperation and dyeing |
Cationic surfactants | Textile dyeing and finishing |
Sodium chloride | Dyeing of cotton textiles |
Copper | Dyeing of cotton and polyamide |
This is the list of some popular chemicals which are also toxic in nature and their uses.
Ques 3: List harmful chemicals and their eco-friendly substitutes.
Answer : Here we are going to know some harmful chemicals and their eco-friendly substitutes –
.
Chemicals | Applications | Proposed substitutes |
Carbon Tetra Chloride (CTC) | Stain removers | Detergent stain removersDetergent (non-ionic, ethoxylates) and water-miscible solvent (glycol ethers) mixtures |
Pentachlorophenol, formaldehyde | Size preservative | Sodium silicofluoride |
Kerosene | Pigment printing | Water based thickeners |
Sodium dichromate | Oxidation in dyeing | Hydrogen peroxide |
Formaldehyde | Finishing and dye fixing | Polycarboxylic acid, non-formaldehyde products |
Ques 4: What are the Ambient Air Quality and water quality parameters which we have to examine in the textile industry?
Answer : At the main gate and near the factory, the industry’s ambient air quality parameters of suspended particulate matter (SPM), SO2, and NOx should be examined. Hot air oven and high volume air sampler chimney spectrophotometer, filters, and impingers to assess the impact on the environment.
The temperature, pH, and total alkalinity are significant characteristics. Biochemical oxygen demand, hardness, and dissolved solids calculating chemical oxygen demand with tools like temperature, pH, TDS, BOD incubator, and COD metres Digestion, etc. are the parameters which are examined to assess the effect on the environment.
Ques 5:Write about the sustainable practices in the textile industry.
Answer : It’s important to think about how long a fabric will endure and whether it can eventually be recycled or composted when it is no longer wearable when selecting a fabric. A fabric passes the criteria and can be regarded as a sustainable option if it was sourced and produced sustainably and has possibilities beyond serving as clothes.
Utilising less water, harmful chemicals, pesticides, and fertilisers, adopting environmentally friendly production techniques, utilising less energy during production, and implementing the 3 Rs—Reduce, Reuse, and Recycle—are all examples of sustainable practices in the textile business. In addition, society is becoming more conscious of green consumption and seeking out eco products. The safety of the manufacturer, the society, the environment, and the consumer are all addressed by sustainability standards and certifications. The criteria were created after careful research, and upon proper application, certificates were granted.
Ques 6: Write about the characteristics of linen.
Answer : Flax is used to make one of the most expensive natural fibre, known as linen. It is made in modest quantities since it requires a lot of labour. However, the unique coolness and freshness of linen cloth in hot weather makes it highly prized. It contains 30% pectin, ash, woody tissue, and moisture and contains 70% cellulose.
Characteristics
- Highest-quality vegetable fibre
- Easily creases due to poor elasticity
- High absorption, relatively smooth, softens after washing
- A good heat conductor and a cooling sensation
- Lustrous
Ques 7: What are some of the things that the textile industry is polluting because of?
Answer : The textile industry’s sustainability may be negatively impacted by the following factors:
- using hazardous substances.
- drinking water
- use of energy
- generating waste
- CO2 emissions.
- Transportation.
- supplies for packaging
Ques 8:What is spinning in the manufacturing process?
Answer : The process of turning textile fibres and filaments into yarn is called spinning. Natural fibres have been manually spun into yarn for thousands of years. Depending on the type of yarn being produced, spinning nowadays uses a variety of techniques and equipment.
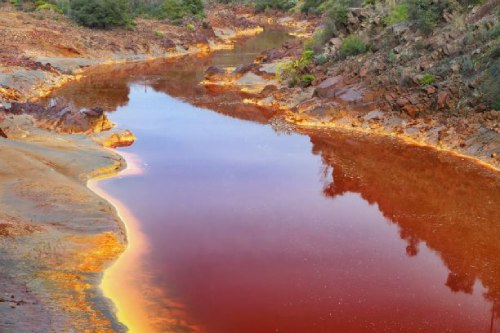
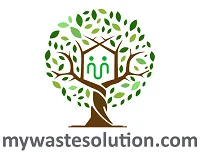